How to Make Data More Useful for Manufacturers
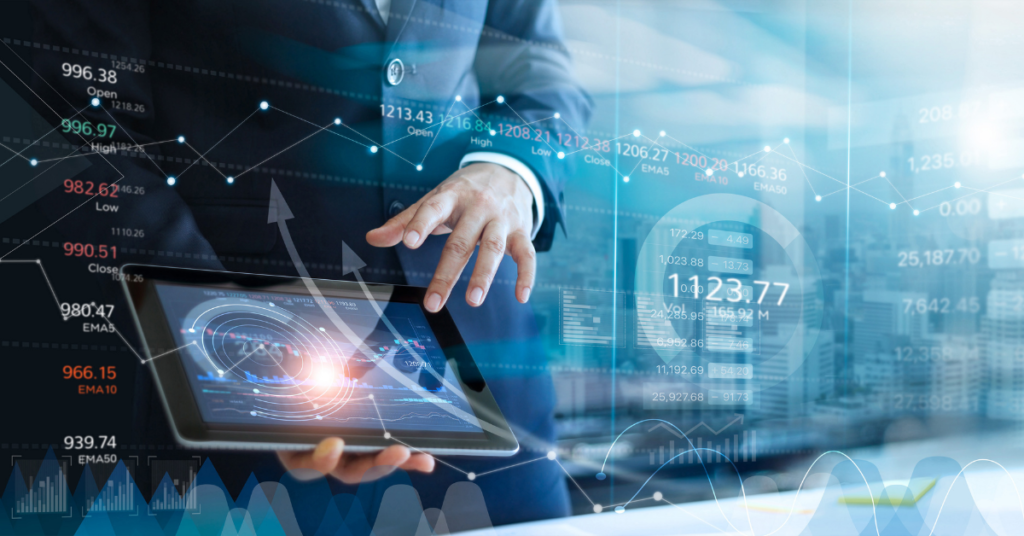
Even if it’s useful, all the data in the world means very little to your manufacturing plant if you don’t know how to maximize its value.
More specifically, manufacturing plants want to use machine learning and other analytics to fine-tune their operations. But many companies in the industry have yet to take the necessary steps.
This blog will explore why companies aren’t embracing data. It will also examine how these solutions are impacting change:
What Challenges Are Manufacturing Plants Facing with Data Usage?
According to Industry Today, the following challenges face manufacturers who want to better use their data:
First, remote systems holding data are often decades old and run on tribal knowledge from onsite experts. And trying to access this information can be trying and labor-intensive.
Furthermore, company data is often disconnected because it’s on separate systems that gather the data in their own unique ways.
On the above note, 38% of surveyed manufacturers claim that integrating reliable systems with varying data sources is their main challenge in meeting quality-based goals. Incompatible data formats often provide information that clashes.
There’s also lacking wiggle room for teams to experiment and hone through a results-based approach.
Lastly, visibility is an issue. Teams can’t access incoming, real-time data to take appropriate actions driven by goals.
What Type of Solutions Are in Play?
The top manufacturers in the industry have found a way to manage the above problems through an approach called “connected manufacturing.”
In short, through this new approach, manufacturers are using analytics, machine learning, and cloud computing to increase transparency, efficiency, customer relationships, and control.
Here are some data analytics, machine learning-based use cases, as outlined by Cloudera.com:
Process monitoring in real-time:
● Offers teams a consistent real-time look into operations
● Provides rich insights into critical sensor parameters and KPIs
● Measures production targets (e.g., production rates, defect rates, cycle time)
Predictive maintenance:
● Provides a real-time look into equipment conditions (via sensor data), so manufacturers can proactively maintain their machines and improve performance
● Combines sensor data with informational technology data (e.g., ERP, MES), helping optimize downtime scheduling and lessen the cost of logistics
Quality assurance via computer vision:
● Automates visual inspections beyond the abilities of humans, so computers can manage quality assurance and reduce the related costs
● Prevents defects throughout the manufacturing process
Throughput optimization:
● Flags and gets rid of bottlenecks while reducing inventory and improving asset utilization
Supply chain optimization:
● Provides inventory visibility and real-time inventory transformation
Which Manufacturers Are Maximizing their Available Data?
PepsiCo is the first data-driven manufacturer that comes to mind.
Pepsi began using analytics software to track soda flavor distribution to stop shipping out too many products. They’d been running into an issue where drinks were expiring before being consumed. As a result of this new approach, Pepsi was then able to reduce shipments and waste.
Another example is Amazon, whose automation investment turned its fulfillment centers into connected ecosystems. Amazon’s data-driven manufacturing innovations cut supply chain planning costs and drove further profits.
What’s Stopping Manufacturers from Buying In?
Amazon and Pepsi show how much positive difference data can make for manufacturers.
Yet, only 31% of manufacturers see themselves as genuinely data-driven. This absence of progress is due to a lack of leadership buy-in, according to Throughput Inc.
We can only surmise that leaders don’t want to commit because of how expensive investing in the equipment can be. Plus, they don’t have the talent to leverage such technology. Without the know-how, investing in these new tools would cause severe financial damage.
Getting the most out of data-driven connected manufacturing requires forward-thinking talent at the cutting edge of the industry.
Fortunately, you can find those top-performing manufacturing professionals at RHM Staffing. Contact us today to find out more.